Webinar
Digitizing the Construction Industry
What You Will Learn
Ever wondered why the construction industry has responded differently to technology than other industries? This webinar discusses the current state of the construction sector and explores key contributors to lagging productivity including the role that software plays in bridging the gap of digitization.
- How leaders and stakeholders are addressing shifts in processes
- Where the construction market is headed and trends to watch
- Catalysts that are creating an opportunity for adopting technology
Speakers
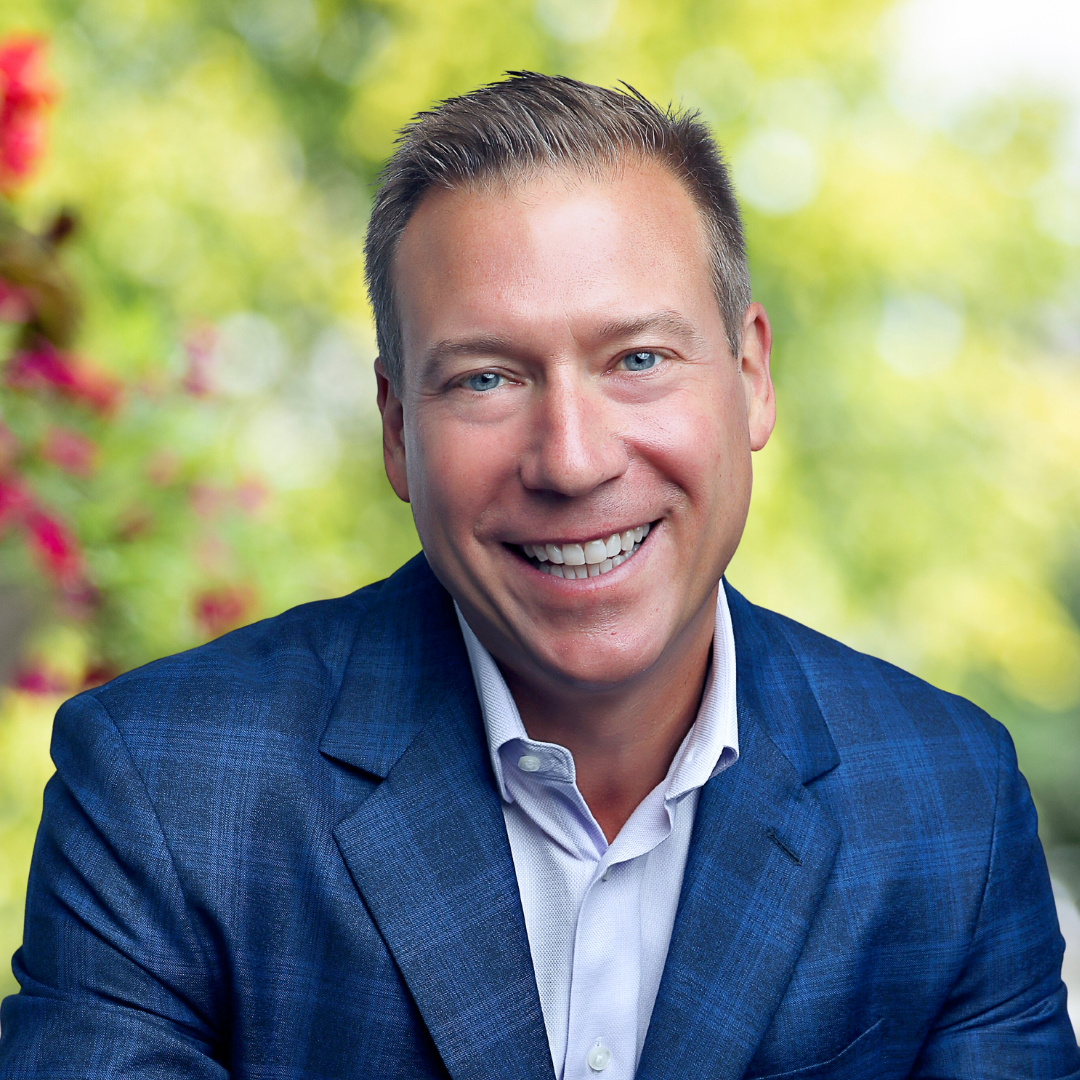
Ryan Kubacki
CEO, Contruent
Ryan Kubacki is currently the Chief Executive Officer of Contruent, the global leader of enterprise project controls software. Ryan was recruited into the role by growth equity company M33 Growth and is a co-investor in the business.
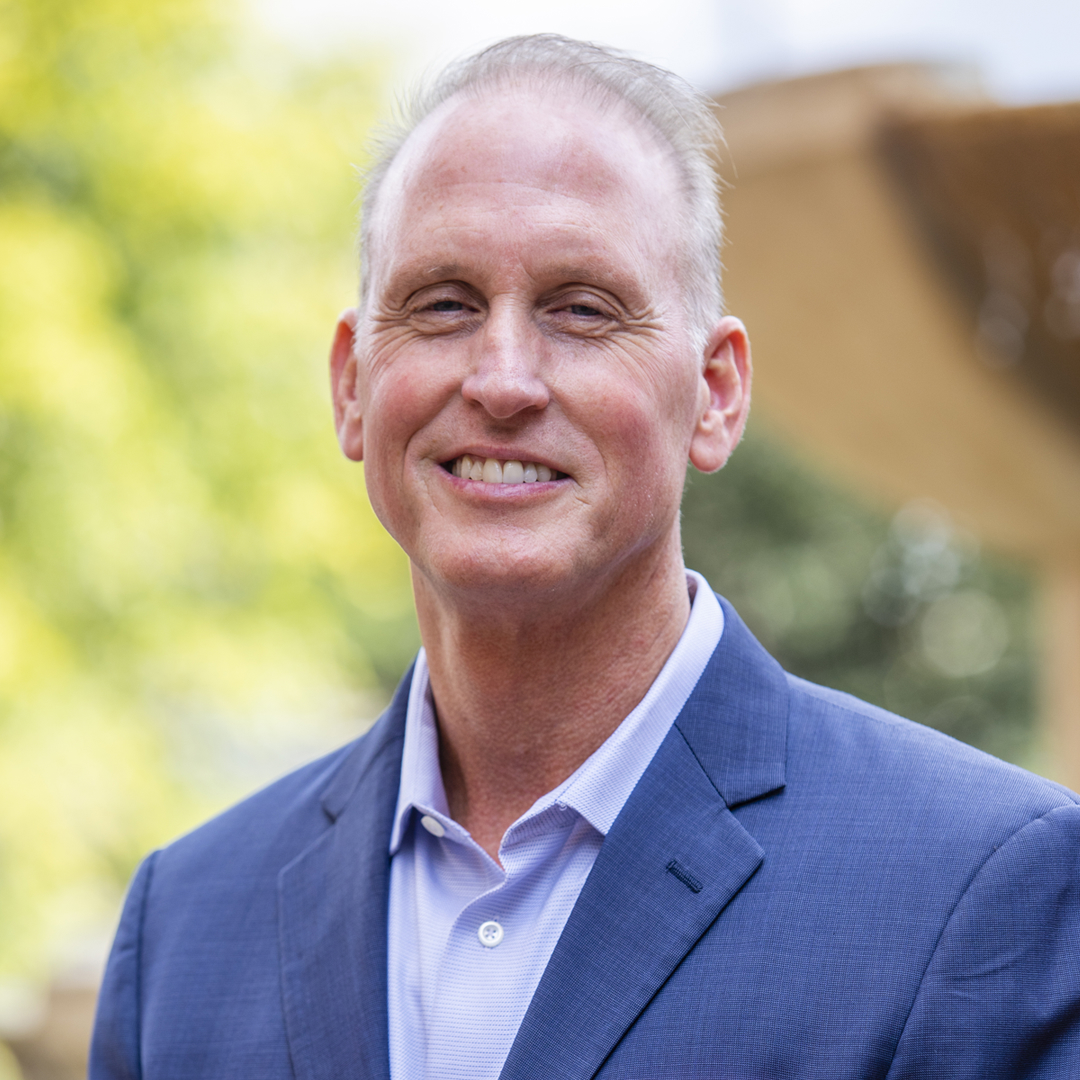
Karl Vantine
CCO, Contruent
Karl Vantine is one of Contruent’s legacy employees and holds decades of global experience in implementing project controls best practices and adopting new software systems that improve business processes. His deep industry knowledge provides the perspective that makes him an effective Chief Customer Officer.
Watch Now
Transcript
Show the full transcript
Moderator (Tiffany):
All right. Well, hello, everyone, and welcome to our live webinar on digitizing the construction industry. In this webinar, we’ll explore the current state of digitization, large capital projects, and some key success factors for increasing digitization. Before we get started today, a couple of quick announcements. All lines are muted to prevent background noise. But if you have a question during the presentation, we welcome that. Please type your question in the Q&A box on the menu, and we’ll get that answered if we have time at the end. Also, this webinar is being recorded and will be sent out to all webinar registrants and attendees. And finally, we want to keep this webinar engaging and interesting. So, a quick heads up: we will have a couple of anonymous polls to gain real-life perspectives from our webinar attendees.
Okay, with that, it’s my pleasure to introduce our two speakers for today’s presentation. Ryan Kubacki, CEO at Contruent, and Karl Vantine, CCO at Contruent. Take it away, gentlemen.
Ryan Kubacki:
Great. Hey, thanks so much, Tiffany. It’s great to be with you, Karl, and our extended community, looking forward to a fun discussion. Perhaps this can sometimes characterize the state of things, right? All of us are doing very important things, and many of you are on point. To build the world’s infrastructure or other large important projects, often there’s people’s safety at stake. And it’s easy to put your head down and get too busy, you know, and not see opportunities to actually improve the very things you’re trying to do. And so this is kind of a lighthearted way to say, hey, we have some round wheels for you. Hopefully, you’re not too busy.
Just real quick, before we get going, many of you have known us as ARES Prism. We rebranded as of January 31; we’re now Contruent, you know, signaling to the market a lot of new innovation that we’re bringing, including the new offering, Contruent Enterprise that I encourage you to speak to us about if you haven’t already done so.
So we’re looking forward to jumping in. So three topics today, right? We want to talk about what is going on with large capital projects. And that’s really what the Contruent focus has been: the larger projects, where more sophistication is required. What is happening with the adoption of software and automation? And secondly, if you’re going through that process of thinking about how to automate, what are some important things to understand that have to be in place, and what are the key success factors for that digitization? Lastly, we clearly will save it for the end. So it won’t be a long pitch. But we want to talk to you about how we could uniquely help you digitize, and we’d love to have those discussions and engagements.
All right, let’s jump into the current state of digitization. And I’m going to tee this up with the current state. And I handed it over to Karl Vantine, our chief customer officer, who’s one of the world’s authorities and experts on very large capital projects. So we’re excited to have Karl here. And he’ll take you through, you know, some of the important details here. So we’re going to open up with a poll question. All right, let’s see who’s paying attention. What percentage of large capital projects are delivered on time and on budget? What do you guys think? Go ahead.
Let’s see, kind of a pessimistic crowd here. No, it’s an optimistic crowd. So what percent are actually on time and on budget? In large capital, I mean, there’s, you know, 100 million above, let’s call it budget-wise.
All right, it looks like people have spoken. So 81% of you think it’s 25%, 14% of you think 55%, 6% think 75%, and none of you thought 90%. The actual answer is 55%. So we need to internalize that we do have an issue with these larger projects. You know, things are not being done on time. About half of them are right. On average, you can see projects have about a 27% cost overrun; that’s real money, especially for some of you working on projects well over a billion dollars, right? We talked about ones not being on time. And projects are almost four times as likely to fail if you haven’t integrated any of your systems and processes and get to that automation.
So clearly, we have a problem. And the problem is somewhat unique to construction because every other sector on the planet has adopted automation and digitization at a much higher level. This is a busy slide. It’s from McKinsey. It just talks about, you know, we’re entering what many people call the Fourth Industrial Revolution. And that’s where we’re seeing unprecedented leaps of productivity and efficiency. In every sector, think about what’s going on with our entertainment, obviously, with streaming, talk about the mobile devices that have changed the way many of us bank. Think about every industry that is there, has really seen an increase in productivity almost exclusively because of rapid technology advancements, particularly software.
That being said, the construction industry, you know, has been slow to digitize, right? 57% of firms, you know, have spent less than 2% of their total revenue on IT and software, that’s not a large investment, right? About half spend about half as much as others, the global industry average. And only about a quarter, 25% of the companies even have a software and digital strategy. So the question becomes, why?
So why do you think the construction industry has been slow to digitize for large capital projects? And here are a couple of prompts: manual processes, the complexity of it all, just the sheer number of suppliers. Perhaps there are other reasons you can say out loud or write down in your notebook or on your OneNote. Give you a second here.
It looks like about 40% talk about just the manual nature of the industry, about 14% are talking about the complexity and the data, about 25% of you are talking about just the sheer number of suppliers, and then almost about 17% are talking about a lot of other reasons. Well, I would say all of those are, for sure, good reasons. And when you think about it, you know, first of all, there are some points that I would mention.
One is the construction industry isn’t really a single industry, right? You have different subsets, whether it’s residential, commercial, civil, or specialty contracting, right? And many of you on the call are in different elements of that, whether you’re, and then at the same time, there are different stakeholders, right? Some of you are budget owners, some of you are general contractors, some of you are architects, engineers, EPCs, specialty contractors, and other important vendors playing a key role. There is a lot of complexity, which makes things harder.
The lifecycle is also long and complex, right? You have the planning phase, pre-construction, then you have to go get all of your materials and procurement, and you actually have to do the construction itself. Meanwhile, you’re trying to deal with operations and disposal, and then you go right back into concept and design, and it just never ends. There’s a lot of it, and elements of that lifecycle have done a better job than others on digitizing, right? And then there are other factors limiting productivity, whether it be just how time-consuming things are. There hasn’t been very clear data sources, so it’s difficult to find one single version of the truth. You know, version control is a problem, and it goes on and on. And I’m sure there are others that you could name.
A couple of other points real quick: Oftentimes, the executive in charge of the budget isn’t always aligned with the folks who are actually out there doing some of the work. And Karl and I did a whole webinar on that in December if you wanted to go back and talk about it. Why is there a disconnect between, sometimes, executive decision-makers and project control experts, right? And there are a lot of different reasons, right. And I think it’s important that we kind of step back and just admit, you know, in summary, construction is hard. And there are very valid reasons people talk about construction and agriculture as sort of the last frontiers to digitize for a lot of good reasons. The ones I mentioned, also just pure bandwidth, you know, the power of mobile devices that are important when you’re on sites and out of an office. And so there are a lot of good reasons, right?
So now let’s get into the meat of it, you know, what are some of the things that have to be in place in order to digitize because the payoff is worth it. So over to you, Karl, I appreciate your time and expertise.
Karl Vantine:
Okay, thank you. Thanks very much, Ryan, and hello to everybody on the call.
So we’re going to talk a little bit about some of the success factors in increasing digitization. And there are a lot of folks on this call with a lot of experience and expertise. I’ve been fortunate to work on many capital programs around the world. There are certainly more than four success factors—there are plenty, and we welcome suggestions on that as well. But these are four that we’re seeing, and that I’m seeing in my travels to visit different programs that are trends around digitization.
There are four technology trends: one is the common data environment, two is data visualization, three is automated workflows, and four is supply chain management. I’m going to talk about each of these four things. Those are the technology aspects. But there’s a common thread here, that you have to tie the technology to the business outcome in order for that technology to be successful. So if you’ll notice along the top, we’ve taken those technology items, and we also talk about the desired business outcomes. So that ties to what Ryan was talking about in order to overcome organizational change management and make sure you’re solving problems at both the budget owner and the executive level, as well as the practitioner level. The budget owner wants to optimize project spend and performance. So that’s a desired business outcome, and to achieve that, the common data environment in the technology world helps do that.
As you work your way across, it’s the same thing. There’s a need to improve visibility and make informed decisions. There’s some technology focus out there that will talk about data visualization. But it’s about connecting stakeholders and solving problems at various levels of the organization. If you’re going to manage change and maximize efficiency for desired business outcome number three, you need some workflows.
And there’s a common theme emerging here: you’re trying to connect various stakeholders throughout the various stages of a project lifecycle. So think about that complexity that Ryan was explaining a few minutes ago, all the different stakeholders involved in delivering the project, different folks in the supply chain, different levels involved, as well as different engineering disciplines, for example.
So the last piece is not just within your business. If you’re an owner and EPC, it’s not just connecting those players within your business. It’s about external collaboration or connection. So supply chain collaboration. These are four of the success factors and trends that we’re seeing out there in the industry right now. So, moving on to the next.
So just start with the first one. Common data environments, what I mean by common data environments, is a term that’s becoming more popular. It’s the evolution of Data Lakes. There’s a lot of data out there, overwhelming volumes of data available to us now. And of course, that can create, as most of you have probably seen, something similar to the graphic on the right-hand side that can create a mess, a data swamp. And so Data Lakes were a big thing in recent years about trying to pull that data together, clean that data up, filter out any garbage data and make it more presentable and usable to the end consumer.
But common data environments have gone a step further now. And they’re not just focused on the Data Lake. They’re also focused on how we create a story? How do we ensure there’s connectivity with that data across the various stakeholders and the various stages of the lifecycle, and then also an involved system? So instead of just a data warehouse or a Data Lake, it’s pulling together the different functions and making sure there’s a story and a thread across all the data.
It’s an interesting problem that’s out there. I’ve seen a lot of consulting efforts along the way to tackle the problem, often custom consulting efforts. And I think that the trick is going to be to try to standardize an approach to common data environments. But that’s one big technology theme that’s out there right now. And I think it’s going to be key to making sure that we improve how we deliver capital projects, is having good, solid, clean common data environments.
If the goal of a common data environment is to create a thread that is often referred to as a golden thread and some traceability of data through the various stages of the project lifecycle, data visualization is about making that story easy to understand. And it’s not just easy to understand; it’s not just about dashboarding and analytics, whether it be Power BI or some other platform. It’s also about making the story easy to contribute to. So, we’re seeing out in the field with our customers that data visualization is more than dashboards. It’s also the more advanced use of your smartphone. Everybody has a smartphone; everybody’s using that to manage their life and their interaction with friends. It’s showing up more now in the construction world, not just for entering data, but for example, for capturing pictures and getting field progress and feeding that back into a core system. So, it’s making the story easier to understand and easier to contribute to.
That includes things like BIM visualization of data. It used to be that 2D picture with the thing on a dashboard. Now we’re seeing more use of 3D, 4D, and 5D, which is a specialty for us, including cost and schedule. And some folks, sure, there are some BIM folks on this call, who would argue whether 6D and 7D are valid terms, but we’re starting to see sustainability and carbon capture and environmental concerns show up as 7D. And that, like all other data, is more easily consumed and more easily contributed to the story if you can do it visually. And then Digital Twin is the last thing that we’re seeing quite a lot out there. It’s early days for Digital Twin, it’s newer. It’s not as broadly adopted yet. But we think it’s got an interesting future.
So, workflows. I realize that on the phone, there are a lot of folks, and you might think, well, workflows aren’t new. People have seen workflows or done workflows in business for years. I’ve had my timesheets approved, and people have had expense reports approved. But I think, judging by the answers to the poll earlier and the number of answers around manual processes being one of the challenges to digitization, that there are also a lot of folks who would agree that in the project world, digitization and automation of workflows haven’t caught on enough yet.
So for things like contract startup, for submitting progress claims, or managing change, handling payment certificates, there’s still just an awful lot of manual work going on out there. And it takes a lot of time, and it sucks up a lot of resources. And it’s ripe for error. So, we’re seeing a lot of effort out there right now to improve automated workflows.
And then the last component of that is, if you go ahead, please, is not just automated workflows again, within the business whether again, whether you’re an owner, an EPC, or contractor, but it’s engaging the supply chain. So it’s between businesses, creating that communication between two different businesses and sharing data used to be, and I’ve been in this business for a number of years. So I saw the emergence of some of that supply chain collaboration. It was previously focused on pre-award bid phases, response to tenders, and things like that. But I’m seeing it now more focused on execution, and involving the supply chain in the same set of data.
So, in the old days, security was a hard thing, how to share data safely and securely. With the advent of SaaS and some of the new security models, we’re getting better in the industry at protecting that data, segregating that data sharing what should be shared, and what shouldn’t be shared, so that you can actually open up pieces of the same data set for the supply chain to act on, to communicate on, and to make decisions. And what that does then is it just avoids duplication and avoids error, and it reduces the amount of rework that’s involved if you can get people working on the same set of data. And so we’re seeing that at a lot of customers. And I’ll share an example or two of that in a minute.
So, how do we at Contruent help you digitize, and what’s unique about what we do that can help you?
So one of the ways we can help you is obviously through our technology. Along the bottom, we’ve discussed the four things: common data environments, data visualization, automated workflows, and supply chain management. We have robust solutions in each space. But more importantly, it’s about ensuring that the technology is adopted and that people find value in it. We don’t just provide technology; we also talk business outcomes and, more importantly, return on investment. Focusing on the common data environment, if you get it right and achieve the business outcome of optimizing project spend and performance, we can help you save 2% on annual spending by providing better forecasting, cleaner data, better visibility, and fewer overruns. That has significant value to companies.
Improving your visibility—if you get data visualization right, you have the ability to make more informed decisions. If I told you we could create an 80% reduction in time spent on data collection, entry, and validation, would that be of value to you? I bring up these numbers because we measure the ROI; we have an ROI tool and customers that have engaged with us and used this tool. You actually use the tool to generate your own ROI from implementing some of these capabilities.
We have one customer, a large rail customer. I’ll pause for an example. Then I’ll continue throughout the rest of the flow. This customer is using the workflow component we provide to maximize change, which aligns with business outcome three and engage their supply chain, addressing business outcome four. They utilize this capability, and they’ve managed on a billion-dollar budget to come in 0.04% under budget. Now, reflect on some of the metrics you heard at the beginning of the presentation from Ryan. How many projects were finished on time and on budget? Less than 55%. What’s the average overspend? More than 27%. Coming in 0.04% under on a billion dollars, the 0.04% might not sound like much, but that’s $4 million under budget on a billion dollars. And that was for a one-year budget; the project is a seven-year project. Think about the kind of savings you can achieve by implementing some of these digitization initiatives.
And just one more example at the end, what if I could reduce your contract spend by 1% through better data quality and more reliable reporting? Not just coming in under budget but actually reducing it further. The results are significant if you implement these strategies.
Let’s go ahead. So I’m going to tie this back, of course, to some of the themes we’ve been discussing around the technology. So, common data environments, our system, the Contruent system, is an out-of-the-box common data environment. Remember, I said it’s not just about Data Lakes, and it’s not just the system. It’s about connecting the data across various disciplines.
On the right-hand side, this is just a sampling of our capabilities: cost management, change management, dashboards, contract management. We’re getting the users into a common environment. We’re keeping all that data in a common data repository, and in an out-of-the-box fashion, we’re helping you create that golden thread of traceability throughout the project lifecycle. Why is out-of-the-box important? Well, not just because it’s faster and because you get reports more quickly and can stand it up more quickly, but the out-of-the-box approach also ensures you don’t miss anything.
One of the things I’ve seen in my career is that a lot of projects start these initiatives with a blank canvas. They try to figure out a system approach or have someone develop something in Excel or a new database. They start with a blank canvas, and with the Contruent common data environment, you can’t miss anything. We’ve given you all the workflows you need to consider, all the different datasets you need to think about, the structures, the coding, and we have the reports ready to go. You can tweak things as you go, but we give you all those answers in an out-of-the-box system. We are the out-of-the-box common data environment.
Visualizing the data—again, with dashboards, which is what we’re showing here, we have the dashboards, the capability to visualize the data and render it quickly, and connect it to all the various components in the system that I showed on the prior slide. But the important part here is not just the dashboard; it’s that we have the drill-down and the drill-up capability between the high-level information that’s shown on the screen in the dashboard visualization. It is connected all the way through down to the end user. This is crucial because, in order to digitize successfully, there are many point solutions out there, but they don’t always stick. They’re not always connected, and they don’t always solve problems for multiple stakeholders. So, they end up being shelfware.
If we get the data connected, like we do with Contruent, and you connect the stakeholders at the top level and the bottom level, then you’re overcoming the challenge of adoption and organizational change management. If the boss is in the system, and the users are in the system, and they’re communicating about the same set of information, you’re going to get digitization that works and sticks.
Back to workflows—specifically, change management. I mentioned earlier workflows around several different artifacts, including payments, certificates, and invoice approvals. This particular example is about change management. Instead of just discussing what’s neat on the slide, I’ll relate it back to what some of the answers were on the poll.
Manual processes were identified as one of the challenges in digitization. We developed our change management system for a large government customer who was dealing with a $15 billion program and handling change management manually. And when I say manually, I mean they weren’t just using email and Word documents; they were dealing with paper forms in triplicate, walking around the office, and getting signature approvals.
Even in this day and age, we were witnessing that. We developed the change management workflows and capability that are shown on the screen, completely replaced that process in that system, and saved weeks of effort and manual labor. We also improved the time for them to close their periods, to approve changes, and created better visibility. This is just one example of the types of workflows that Contruent can help you with.
And as I’ve mentioned a few times now, it’s not just about improving workflows within your business. It’s also about enhancing collaboration and coordination with the supply chain. Within the Contruent system, we have a contractor portal that provides visibility and creates the opportunity for the supply chain to act on the same data set used within the project. This reduces rework, eliminates mistakes, and shared visibility drives more collaboration and, frankly, just speeds things up, making it more efficient.
You can’t tell from my red and blue background for Contruent right now, but I’m actually traveling. I just spent the last three days with two large infrastructure customers who are developing significant programs. They’re helping us build this capability out even further so they can enhance collaboration and pull the supply chain in closer. This is something that might interest you, and we’d like to engage on this topic. We’d like to share their stories. These customers are happy to talk to other customers and explain what they’re doing and how it works. So, engage with us, and we’d like to get your thoughts on this as well.
Our mission is precision delivered with speed and accuracy. We are faster to deliver because we’re out of the box and because we have years of experience with all these different technologies and ideas around common data environments and workflows. We’re also interested in where the industry is heading next.
So go ahead next. What’s the next big thing? So if common data environments and workflows and visualization are the big trends and the big themes right now in digitization, where does it go next? And from where I sit? Things that look really exciting to me and that present really interesting opportunities are machine learning. So if we’ve got a common data environment with all this different data out there, can we use machine learning to help improve how we do root cause analysis, how we plan better, how we incorporate lessons learned from years and years of experience and from vast volumes of data to benchmark and incorporate lessons learned back into the next plan. Because a lot of the, as you all know as practitioners on the phone, a lot of the problems if you get them wrong in planning, they just continue on throughout the evolution. And you can never really catch up if you get it wrong in planning. So can we use machine learning to do better plans?
And building on that theme: Artificial Intelligence? This is something that’s starting to show up more in conversation. It’s been said that if a computer can think, can it actually be taught to think better than humans? Meaning, can it eliminate some of the things that we get wrong when we’re planning out these large capital programs? Can we eliminate planning biases? Can we get rid of false optimism? Can we take advantage of the lessons learned and really apply them correctly so that our plans are more realistic, so that we start to eliminate some of those metrics of every project is over budget? Well, we’ll get the budgets right from the beginning.
Then we’ll execute again with that digitization and some of these strategies so that we start reducing some of those, some of those overruns, and we start solving those problems that Ryan talked about. We’re curious to hear your opinion on things like Digital Twin in virtual reality. Virtual reality: can it be used to improve design, safety, or training? Can Digital Twin help with displaying progress more effectively? So that as I said earlier, we’re talking visualization so that you can contribute and understand the story more easily when you’re communicating with the various stakeholders. So these things I think you’re taking off, I think they’re right for takeoff. But curious to hear your opinion.
So we have one last poll for you. We’d like to hear your ideas. There are a lot of folks on the call from various aspects of the industry. We’d like to hear your opinion on where you think it’s headed and what’s next. And maybe more importantly than the poll, we’d like to engage with you and talk about those things so that we focus our investment in the areas that you all believe are important as customers.
So, unlike the last poll, Tiffany, I can’t actually see what the answers are here.
Moderator (Tiffany):
They will be released in just a moment as people are still filling them in, and then we’ll display the results here shortly.
Karl Vantine:
Okay.
Moderator (Tiffany):
Just a couple more moments here.
Karl Vantine:
The other polls show a little tally of who’s winning throughout.
Moderator (Tiffany):
This one’s asking them to fill in a blank. So I think that’s what’s different here. All right. I think we’ve got just a couple more coming in. Great job, everyone. Oh, lots of answers coming in now. Alright, here we go. Let’s go ahead and end the poll and share some results.
Ryan Kubacki:
Maybe read them out. I don’t know if we can see them.
Moderator (Tiffany):
Yes, I will read them out for you. Okay, so one of them is software for Lean construction. Another is the development of a program management approach for infrastructure. Another is Digital Twins, AI, BIM and Digital Twin, digitalization artificial intelligence, and machine learning. Lots of interesting ones. Virtual Reality, robotics, again, with AI, and 3D printing. A lot of people agree with your topics here of artificial intelligence, machine learning, BIM, and virtual reality. So thank you, everyone, for participating.
Karl Vantine:
I think, in hindsight, I wish I had asked a better question, and we can follow up with the folks who answered artificial intelligence and machine learning. We can follow up with everybody who had a question or who contributed. But the question is how could something like artificial intelligence be best applied so that we can improve the way we do things in this industry? That’s a dialogue that, for me anyway, is quite a lot of fun and would love to engage in.
Ryan Kubacki:
That’s great. Well, hey, I always appreciate your insight, Karl, so hopefully now people feel like you can say thank you. At Contruent, we’re not too busy. If you want to check out the new innovation, the new wheels, we’d love for you to engage with our teams and our experts. We also not only have new software having been launched, but we have an extensive and direct services team, almost comprised of people almost exclusively having been project managers of large capital construction companies. So we do bring in 25 years of hundreds and hundreds of large capital project experience at your service. So, you know, I think with that, we’ll wrap it up. And, you know, Tiffany, if you want to let people know how to do the questions we have, we’ve got plenty of time for some good questions and answers.
Moderator (Tiffany):
Absolutely. If you have a question, feel free to enter it now. Use the Q&A box below in the menu. We already have some questions entered, so I’ll go ahead and start us off with the first one. Does Contruent have BIM 5D integrated into the software?
Karl Vantine:
We do, we do. We have an estimating platform that includes both scheduling and cost, which is my definition of 5D. So, yes, we do have that.
Moderator:
What about Digital Threads?
Karl Vantine:
I’m not sure what that is. What is a digital thread that’s different than, say, the golden thread? I guess if we can engage, someone can actually start to answer my question. If that’s the golden thread where we create traceability through the data set as it moves throughout the project lifecycle, then yes, that is what we’ve talked about.
Moderator:
The next question is, given that agile PM principles and frameworks such as Scrum are being implemented more in civil engineering, what tools would you recommend to manage those approaches?
Karl Vantine:
Well, I’d be remiss if I didn’t recommend our own tool. So one of the things I know that’s a cheeky answer, but one of the things about our tool is that it can accommodate different approaches, whether it’s Agile, Scrum, or any different framework. So, we are out of the box, but it is a configurable system. So you can configure your coding structures, you can configure your approach, and you can configure the timescales when you require answers back. So, whichever framework you’re trying to apply, you can actually configure into the system. So, I obviously recommend ours.
Moderator:
The next one is I believe in digitization in the construction industry and would like to cooperate with you in the future. I implemented a PMO in the construction industry before. So, we got some experts here on the call, which is great.
Ryan Kubacki:
Email us. We’re always hiring, by the way. So here’s our email address. It’s right there.
Karl Vantine:
There were almost 100 registered. So, I imagine we have 100 experts, various parts of it.
Moderator:
All right, digital threads. A little bit more of an explanation here. Digital threads are all records linked to Digital Twins, including project delivery records.
Karl Vantine:
Okay, so we have the datasets. How closely is it linked to the Digital Twin piece? We’re not as far down that path, but we have the datasets that support that. Sure.
Moderator:
Alright, I think that is all of our questions that have been inputted. We want to thank you all for joining us today for a webinar on digitizing the construction industry. And thank you to our two presenters, Ryan and Karl, for leading us through this discussion. This webinar is one of a series, so we will keep you updated on upcoming webinars in the future. And if you have any questions that weren’t answered today, engage with us. Feel free to check out our brand-new website, email us at info@congruent.com, or contact our speakers directly. We hope that you had a wonderful time joining us and have a wonderful rest of the day. Thank you, everyone.